Design criteria vacuum cleaners
When designing an industrial vacuum cleaner, a large number of things affect whether or not it functions successfully in practice. TNO has drawn up guidelines that can serve as a guideline for designing good vacuum cleaners. The main points are listed below.
Download hier de uitgebreide richtlijnen (pdf) >> (Dutch)
Flow / airflow industrial vacuum cleaner
As a rule, the airflow through the extraction hose should be as high as possible. In concrete terms, the following points apply to an industrial vacuum cleaner:
- A flow, measured at the end of the suction hose, of at least 150 m³/hour is desirable
- A larger hose diameter is better than a smaller hose diameter (Ø 50 mm, flow unchanged; Ø 38 mm, flow decreases by 25%; Ø 19 mm, flow decreases by 65%)
- Shorter hoses are better than longer hoses (standard 3-5 meters)
- A smooth inside of the hose is better than a rough/ribbed inside
L- and M-classifications
There are two classifications, the first is the classification of the (dust) filter of the industrial vacuum cleaner. This classification indicates the filter effectiveness of the relevant (dust) filter.
- A L-filter has an efficiency of 99 %.
- A M-filter has an efficiency of 99,9%.
- A H-filter has an efficiency of 99,995%
Most industrial vacuum cleaners nowadays contain at least an M filter.
In addition, there is the classification of the vacuum cleaner:
- L-classification: the vacuum cleaner has NO alarm system (light or sound signal).
- M-classification: the vacuum cleaner DOES have an alarm system (light or sound signal).
- The alarm system is activated when the suction capacity of the vacuum cleaner is too low. An L-class vacuum cleaner can also contain an M-filter.
Filter cleaning
There are a number of filter concepts, namely:
- Three-stage filter system (cyclone, fine filter, H/HEPA filter)
- Single filter system (L,M,H)
- Disposable filtersystem
Contamination of dust filters has a major impact on the capacity of the vacuum cleaner. The most important design criterion is therefore to ensure that the dust filters do not become dirty too quickly. This can be achieved by applying:
- Mechanical cleaning (vibration)
- Reverse pulse cleaning (air reversal)
- Regular replacement of filters and/or dust collection filters
- Use pre-separators (cyclones)
During filter cleaning, the suction function of the vacuum cleaner must be ensured: while half of the filter is being cleaned, air is drawn in through the second half. It is also recommended to continuously check the operation of the vacuum cleaner by means of a flow indicator (acoustic, visual).
Dust collection industrial vacuum cleaner
There are a number of options for dust collection:
- Open container
- Open plastic bag
- Closed paper bag
- Closed plastic bag
The open systems have the disadvantage of extra pollution of the filter systems. The closed papers/plastics become dirty during use and thus cause a reduction in the effective extraction capacity of the vacuum cleaners. An advantage is of course the reduced dust load for the L, M and H filters. When removing these closed systems, full of dust, the exposure to harmful dust is very low, in contrast to open systems.
Compartment
The use of vacuum cleaners and the compartmentalization are communicating vessels. With complete compartmentalization of the dust source, the dust cannot spread to the immediate working environment. Incomplete compartmentalisation may cause dust to spread into the working environment. The degree of compartmentalisation places different demands on the extraction capacity of vacuum cleaners.
The image below shows examples of closed systems, semi-closed systems and open systems.
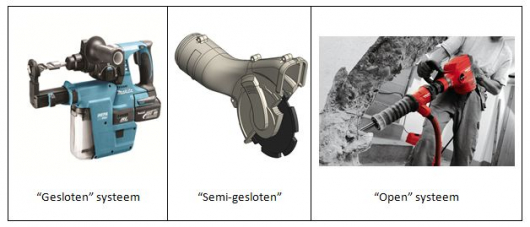
The closed system is completely compartmentalized around the dust source; with the “semi-closed” system in the extractor hood for an angle grinder, there is partial enclosure of the dust source and an unambiguous direction of distribution of the dust. With an “open” system, such as with the chipper, there is a considerable distance between the source and the extraction hose. The choice of a vacuum cleaner partly depends on the degree of compartmentalisation. The blue hammer drill functions dust-free with an extraction capacity of approximately 20 m3/hour. The angle grinder with extractor hood works dust-free with a capacity of 150 m3/h. The chipping hammer shown works dust-free when using a vacuum cleaner with a capacity of more than 250 m3/hour.
The complete system (tools, extraction module, vacuum cleaner) determines the ultimate exposure to dust in the breathing zone of the employee. The better the compartmentalisation means less demands on the vacuum cleaner.